Laser Welding
Dutton Engineering Metal Fabrication Service
Laser Welding What Is It
Laser welding is a highly precise process that uses the energy of a laser beam to heat and fuse materials together. The laser’s heat melts the surfaces of the parts, forming a molten weld pool, which solidifies to create a strong, seamless bond. This technique is versatile, allowing for welds of various sizes and depths across a wide range of materials, including metals, dissimilar and reflective materials, and even non-metals.
The process can be performed with or without filler material and can accommodate both narrow and wide joints. By directing the laser in customizable patterns, welds that are significantly wider than the initial laser spot can be achieved. For components that require minimal thermal distortion, laser welding offers excellent control, enabling rapid penetration and welding speeds of several meters per minute. This process is ideal for automation but can also be executed manually using handheld laser welders, providing a faster, more precise alternative to traditional welding methods.
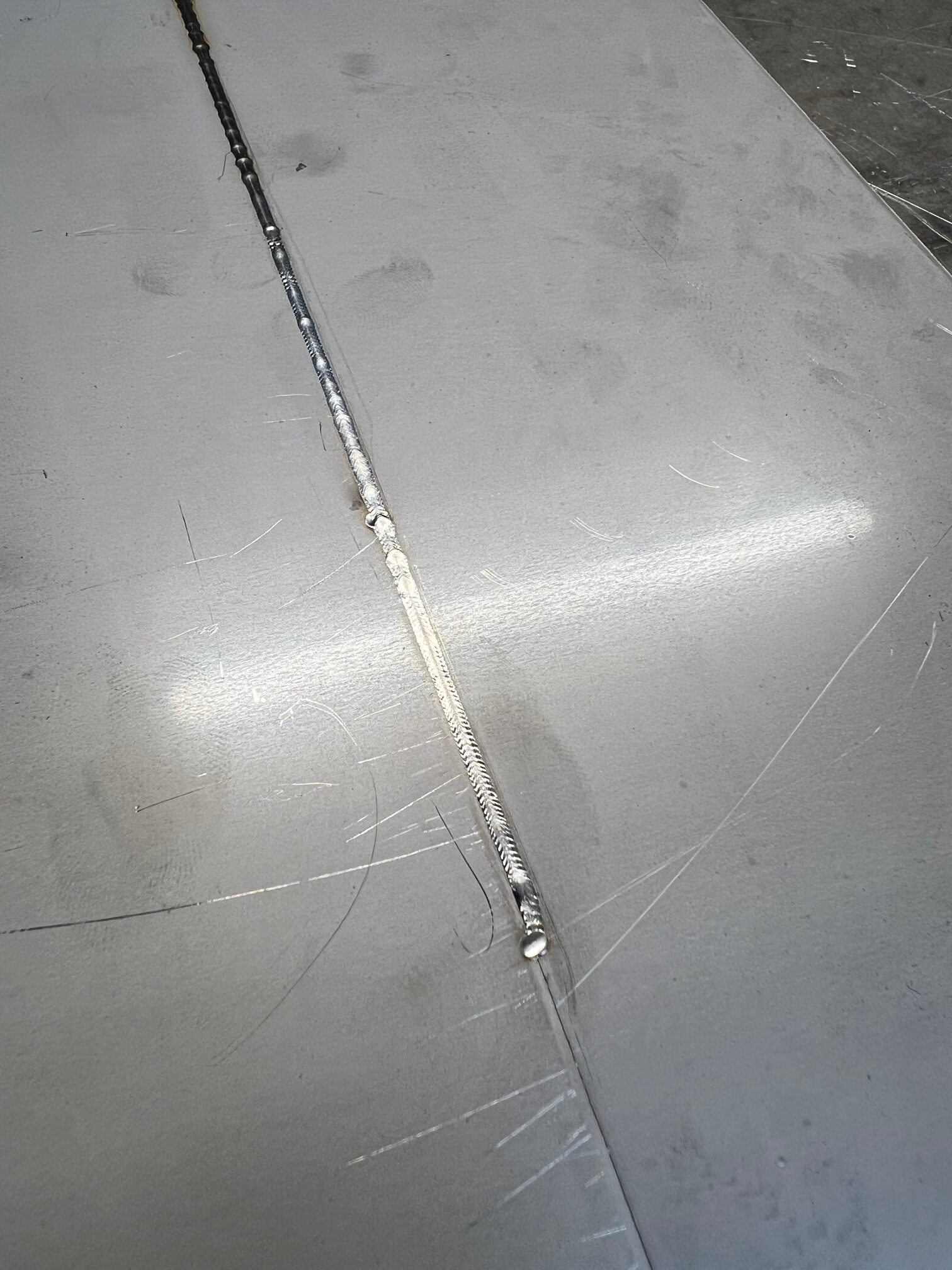
Advantages of Laser Welding
High Welding Speed
Laser beams can be rapidly scanned along the work surface to create simple or complex seam shapes. For many applications, laser welding is significantly faster than alternative welding methods.
High Weld Quality
Laser welding creates exceptionally high-quality joints with excellent physical and electrical properties, even when joining challenging materials like aluminum or dissimilar metals.
High Precision & Repeatability
Laser welding creates a small spot on the part for precise control over the weld pool. As a non-contact process, laser welding experiences virtually no degradation in weld quality.